Copper Molybdenum Copper (CMC) Material
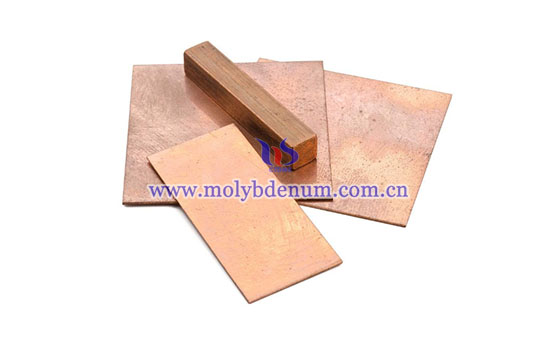
Because copper has a high electrical conductivity, thermal conductivity and molybdenum has a low coefficient of thermal expansion, high strength and other good properties, so the use of both the excellent performance of a composite material highly favored by electronics engineers. Besides, it has a wide range of applications in microelectronics. US Polymetallurgical, Polese, Elcon and other companies using online continuous rolling composite technology and the United States AMAX company and Climax Specialty Metals company using hot rolling complex methods to produce a copper molybdenum copper (CMC) composites material, and applied the relevant patents. In China, some researchers have tested the explosive welding method for CMC electronic packaging production and have studied the adhesion mechanism of CMC encapsulating material interface in detail. Because the physical properties of copper and molybdenum are quite different and they are not mutually solution, so the interface of both copper and molybdenum can closely combine is the key to the preparation of CMC composites material. On the one hand the interface should have high bonding strength and clean surface is an important prerequisite to achieve high strength bonding of interface. On the other hand, if surface is too smooth, it is hard to process deformation and composite strength is lower as well, so the surface state before the composite of molybdenum and copper plate interface to achieve high strength composite material has an extremely important Impact.
Effect of CMC materials main treatment methods are: sandblasting method, steel brush treatment, chemical treatment.
Using hot rolling composite method for CMC production, the rolling temperature is 600 ~ 1000 ℃, copper with high purity copper plate # 1, molybdenum with # 1 pure molybdenum. Surface treatment uses three different methods, namely, sandblasting method, steel brush treatment method, chemical treatment method. Sandblasting method: molybdenum plate after sand blasting then uses chemically treated to remove grit, but copper surface treatment method is chemical treatment; steel brush method refers to molybdenum and copper plates are all processing steel brushing treatment; chemical treatment means molybdenum plate and copper plate only wash by chemical wash. Using SEM, metallographic structure and other methods observe the microstructure of copper and molybdenum’s interfacial bonding.
CMC composite laminates interface average shear strength is 55.9, 66.1 and 78.9 MPa which respectively process by the chemical treatment method, steel brush method and sandblasting method. Obviously the interface shear strength of molybdenum and copper which process by sandblasting method is higher than processing by chemical treatment method and steel brush method. And to improve the interfacial shear strength is important for composite materials’ interfacial bonding. Observing metallographic photomicrographs of sandblasting and chemical treatment method we knew that the after sandblasting method copper and molybdenum interface is rise and fall; but processing by chemical treatment method molybdenum and copper interface is more flat, so the interface bonding strength which processes by sandblasting method is higher. On the other hand, because composite laminate after annealing the anneal temperature is lower than molybdenum recrystallization temperature, but higher than copper recrystallization temperature, so after annealing molybdenum grain is still fiber structure, but copper undergone significant recrystallization and growth. Comparing with chemical treatment methods, processing by sandblasting method the equiaxed grain and annealing twin is smaller and there are more grains on molybdenum and copper interface unit of length. The grain near copper is bigger and has large annealing twin, however it is bad for improving shear strength. For composite materials, which are generally different coefficients of expansion, the heating or cooling, the material with different coefficients of thermal expansion along composite interface the direction and contraction degree is different, resulting in thermal stress. Thermal expansion coefficients of the two materials the greater the difference, the greater the thermal stress generated when such thermal stress reaches a certain level, it will produce micro-cracks, or bubbling on the bonding interface, so serious large-scale separation of interface resulting composite material failure.
Laboratory study of CMC composite laminates are mainly used as support and heat output parts in electronic packaging, and therefore frequently withstand thermal stress cycle. Due to the thermal expansion coefficient of copper is about three times than molybdenum, when heated, the interface thermal stress inevitably very significant, so molybdenum and copper interface must have a high bonding strength, in order to ensure the composite laminates without cracking, and stable and reliable work. CMC composite laminate after blasting treatment has not discovered any bubbling or cracking when it was heated at 850 ℃ and shock chilling. But there are brush bubbling phenomenon occurs when it processes by chemical treatment method and steel brushing method. So using sandblasting method copper molybdenum copper material interface bonding is the best and overall performance is better.